|
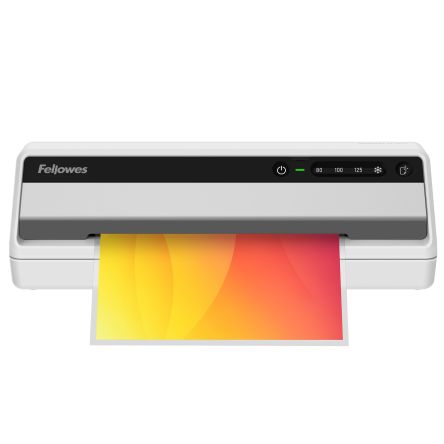
Laminating is primarily a handy way of preserving important documents and papers - this might typically include items such as:
-
-
- Report covers
- Certificates
- Checklists and safety instructions
- ID and business cards
- Restaurant menus
- Photographs
- Posters and signage
-
While many other sorts of documents (as well as non-paper items and surfaces) can be laminated, protecting and embellishing key documents for presentation or display purposes tends to be the most common use of the technology in everyday scenarios for the majority of homes, schools and offices in the UK.
In these sorts of contexts, lamination generally involves attaching a fixed plastic wrapper or cover to the item of paperwork in question, generally for the purposes of safeguarding it against damage and ensuring it stays in pristine condition for as long as possible. The resulting plastic coating around the document can also help to enhance colours and all-round presentability, as well as providing a wipe-clean surface for temporarily marking up the surface using dry-erase pens.
There are lots of different types of laminating machines for sale on today’s market, ranging from small and inexpensive desktop varieties for home and small office use through too much larger and more costly industrial versions. The latter tend to accommodate a wider array of temperature settings and document sizes, and usually feature multiple sets of rollers for helping achieve a flawless finish in more demanding applications.
In broad terms, most laminating machines come in one of three main configurations:
- Film laminators - these machines tend to use two separate layers of laminating film, and incorporate the top layer into the laminator mechanism itself.
-
- Items are placed on a bottom layer of film and fed into the machine, where the hot rollers automatically align and press down a separate top layer as the items are being passed through.
- This type of laminator is often the most flexible and is generally used in large-scale production environments where many (or bigger format) items need to be processed quickly.
-
- Pouch laminators - this is the most common form of desktop-type laminating machine you’re likely to encounter in day-to-day scenarios, very widely used for both at-home laminating projects and in a range of standard office environments.
-
- Pouch laminators must be allowed to heat up to optimal temperature before a document is manually fed through inside a clear plastic pouch or wallet lined with adhesive, which is then pressed together under hot rollers to form a sealed cover.
-
- Cold laminators - Non-heating versions are also available for handling documents or items that might be sensitive to high temperatures, or easily damaged during the standard hot lamination process.
-
- Examples could include items made with types of vinyl or adhesives, carbon copies, some forms of inkjet printing, and certain types of photographs.
- Cold laminators, as the name suggests, use pressure only to seal an adhesive plastic pouch or film around the item being laminated, and are most often configured as small laminating machines for short-run projects or very occasional document preparation.
- Cold laminators tend to be cheaper to buy and run, but the pouches used in this type of machine are often considerably more expensive.
-
In this guide, we’ll look at some of the more common types of machines, lamination pouches and accessories available from UK suppliers. We’ll help you decide what to look for in a laminator, and choose which sorts might be the most useful across a range of particular applications, environments and workloads.
How do laminators work?
A laminator machine typically uses a combination of heat, pressure and an internal roller mechanism to apply a thin plastic cover to paper documents or other items, In the most common scenario, the paperwork in question is fed into the laminating machine one page at a time, sandwiched in loose plastic sheets or lamination pouches.
In the case of most modern pouch laminators, the plastic cover placed around the document being fed into the machine is pre-coated with a special sort of extruded adhesive on all of its inside surfaces. As the pouch is heated under pressure from the machine’s rollers, it helps to bond the two sides of the pouch tightly together across the front and back surfaces, forming a protective cover and seal around all four sides.
Some higher-end laminating machines will allow the user to adjust settings for temperature and feed-through speeds, which can make the job more efficient and effective when dealing with heavier duty pouches or larger work pieces. In addition, some machines have the ability to reverse-feed documents that have become misaligned, often using special sensors that can detect misfeeds and perform this reversal function automatically.
As they perform their heating and pressing function, the laminator’s rollers tend to lose some of their heat as it’s transferred directly into the cardboard carrier and the document pouch - this is why you’ll often have to wait a short time between documents, to allow the rollers to come back up to optimal temperature once again before feeding your next document in. However, most modern laminators heat up very quickly, so there isn’t usually a significant delay required between successive feeds.
Types of laminators
Strictly speaking, lamination technically refers to the process of applying a plastic cover to the surface face of a document or other item. Two-sided lamination, where the plastic cover forms a complete seal all around the document on both the front and reverse sides, is more properly known as ‘encapsulation’.
However, most people use ‘laminating’ as a somewhat catch-all term to mean any form of heat-based plastic coating process, including full sealing of documents in purpose-designed double-sided pouches.
There are numerous types of laminators available for handling different sorts of documents, pouches and workloads. In this section, we’ll take a brief look at some of the more common varieties found in many homes and offices today, and which sorts might be best suited to which type of production environment.
A3 Laminator
An A3 laminator is especially useful in environments where large print materials, such as posters or signage, need to be protected and embellished for display. A3 and larger format laminators are often of the thermal film variety, either single or double-sided, as these tend to offer greater flexibility in terms of item orientation, workpiece size and operating temperature. They’re ideal for producing sealed and protected documents for public display, such as window dressings, public signage or exhibition graphics.
A4 Laminator
A4 laminators are by far the most common format found in the majority of homes, offices, schools and retail environments. They’re particularly widely used for producing report covers, multiple ID or business cards, photo montages, checklists or instruction guides, wipe-clean rotas, menus and other reusable documents that need to stay looking presentable even in constant handling.
Most A4 desktop laminators tend to be the pouch variety, and rely on heated rollers to seal purpose-bought adhesive plastic wallets around the documents in question. More economical varieties usually incorporate a single pair of rollers that pass the paperwork through the laminating machine, while higher-end versions might feature multiple sets of rollers to ensure a cleaner finish with greatly reduced risk of bubbling or misalignment.
Office Use
The key decisions you’ll need to make when choosing a suitable laminator for office use are what size to go for, and also how often you’ll likely be using it. Both A3 and A4 varieties can come at a wide range of prices and specs, but for the most part, the more expensive versions will offer one very key feature over more cost-effective models: speed.
While the initial investment in a top-of-the-line laminator can be much higher than for a budget brand, it may actually work out saving you money in the long run if you’re not constantly having to wait around for slower laminating processes and ramp-up times, or frequently having to re-run the process due to a higher incidence of misalignments and bubbling that you tend to get with very cheap laminators.
Many models intended for more intensive day-to-day school or office use come with handy time-saving features such as built-in memory functions, meaning you don’t have to reprogramme the machine each time you want to use it.
Industrial/Heavy Use
Again, the key decisions when looking to buy heavy duty or industrial laminators will generally come down to the degree of flexibility required, and the intensity of use you expect it to undergo. Heavy duty laminating machines can be built to withstand near-constant use, but you can expect to pay a premium for this sort of durability and consistency of performance.
If you’ll need to laminate multiple items on a daily basis, especially at a high rate per hour, certain higher-end or heavy-duty laminator machines are built to work faster and harder than others, producing superior quality laminations at a much quicker output rate.
Another key consideration will be how long you want your laminated items to last, as this will impact on the type of lamination pouches or films you should buy, and thus ultimately on what sort of machine you’ll need to meet your production demands.
Hot and cold
When it comes to choosing whether to buy a hot or a cold lamination machine, the key differences between the two (apart from the obvious!) really come down to the types of documents you’ll be working with.
Many people feel that, for short-run or occasional use, a cold lamination machine is sufficient for their needs - and in fact cold laminating can result in a nicer-looking document for certain types of ink or printed materials, as the lack of heat makes it far less likely that any running, blurring or colour variance will appear in the final product. Cold laminators also tend to rely on heavier pressure than heated roller versions, meaning that there can be less likelihood of bubbling in higher quality models.
Hot lamination, on the other hand, tends to be a better choice for consistency and durability over more frequent daily use, particularly in environments where speed and repeatability is more important than flawless finishes. The pouches intended for hot lamination use also tend to be considerably cheaper and more widely available than cold versions.
Provided you have a clear understanding of what material and document types are suitable for hot roller laminating, it’s a very straightforward and quick process to protect and embellish many documents in a short space of time with a heat-based machine. Higher-end models also offer numerous additional features for batch-processing, temperature adjustment, programmable memory functions and more.
Laminating photos
A quick word on laminating photographs: it’s one of the more common intended uses for laminating machines generally, but one that many users tend to be (understandably!) worried about.
While photograph lamination is usually done to help preserve the picture for longer, there’s always a perceived element of risk when you can’t easily replace the photo should anything go wrong. The main point to note when laminating photographs is that, as with all laminating machines, higher roller counts will give you better and more consistent results, with far less chance of misfeed or bubbling.
The most budget-conscious laminators will generally come with two rollers, and these can be somewhat inconsistent - far better to go with four-roller models for documents that matter, and in the case of cherished photographs, six rollers or more is even better. These are generally the more expensive models, but as with so many things, high-end photo laminating machines do tend to confirm the old ‘get what you pay for’ adage.
Also be conscious of the film or pouch you’re using for the lamination on important photographs. For the best results, you’ll want to use high-quality film that’s relatively newly made and decide beforehand what’s the most appropriate trade-off for you between the thickness (and thus durability) and consistency/rigidity. Also be mindful of the finish you’re looking for - gloss pouches or matte, smooth or textured - and, for really cherished items, always do a practice run on a blank piece of paper first.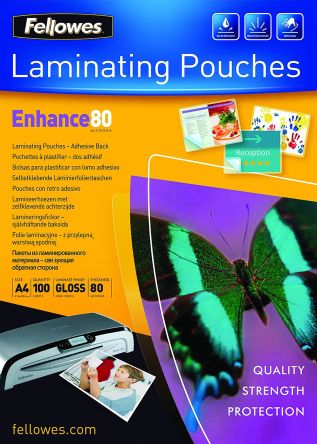
Plastic film
The type of laminating pouch or film you select for any given project will be influenced by various factors. First and foremost, you’ll need to consult your own laminator’s spec sheet to check what are the minimum and maximum thicknesses of film it will accept. These values can either be stated in millimetres or microns.
Secondly, you’ll need to know what you want the finished product to look and feel like, and adjust your film/pouch selection accordingly:
-
-
- 10mm pouches, if your laminating machine can accommodate them, will result in an extremely durable document that is difficult to bend and manipulate.
- Conversely, a 3mm pouch will result in a much more lightweight document that’s easier to work with, but also far more bendable and less robustly protected against damage or environmental challenges.
- Don’t forget that total lamination thickness will usually be double the rated thickness for a single side of the film or pouch, as most projects will tend to be sealed on both sides.
-
Finally, bear in mind the finish you’ll want for the application and environment you’ll be using the document in. Gloss pouches, for example, can look sleek and impressive on report covers and certificates but may prove too reflective to be ideal for public signage in brightly lit areas.
How to use a Laminator
All laminators will come with their own specific step-by-step instructions, and these should always be your first port of call when looking for guidance on how to use a laminating machine. However, there are some broad rules of thumb which are fairly universal, and it pays to know the general workflow for laminating prior to inserting your first document.
When using a pouch-style laminator to seal plastic wallets or films together around an item, the document and its pouch are usually assembled first outside the machine. In some cases, these are then placed inside an additional protective cardboard cover, known as a carrier.
On certain models, this carrier adds an important layer of protection between the hot rollers and the plastic surface, which reduces the chances of the plastic pouch bubbling, clouding or sticking to the rollers as it’s heated. Note, however, that most modern brands of laminating machine no longer require a carrier - it used to be entirely standard, but these days the demand for them is becoming less widespread.
Always check whether the manufacturer of your chosen model recommends a carrier or not, as using them unnecessarily can mean having to perform multiple passes of a single document, when in most cases they ought to require just one. Where they are required, they can sometimes be supplied with the laminating machine itself, but it’s more common to find them included with packs of pouches bought separately.
During the lamination process, the user waits for machine’s rollers to come up to temperature after being switched on and then feeds the document assembled in its pouch - either with or without the cardboard carrier - in through an opening or tray at one side of the machine. As the document passes through the rollers, the plastic pouch around it is heated and pressed together, forming a sealed cover.
Depending on the make and model of laminator you buy, you may find you have to wait a short while between lamination runs so that the rollers can get back up to ideal temperature before the next batch is worked through.
After successfully laminating a document or item, any excess plastic left to form a border around the edges can then be trimmed away once the surface has completely cooled. Never attempt to do this when the item is fresh off the machine, as this can warp or distort the plastic in various ways which will then be very difficult to correct or remove as the sealed pouch hardens.
Summary
Whether opting for an inexpensive personal home-use laminator, ideal for small-batch or project-by-project hobbyist use, or a more hardwearing/heavy duty design intended for heavier office, school or workplace rotation, there are a range of additional considerations and features you’ll need to bear in mind when choosing which type of product or laminating accessories to buy.
For more advice on laminator types, pouch and film selection, installation, use and maintenance, please feel free to contact a member of our expert support team any time.