- Published 15 Mar 2024
- Last Modified 15 Mar 2024
- 5 min
Precision Measuring Instruments in Electronics Manufacturing QA
Explore the pivotal role of precision measuring instruments in enhancing quality assurance within the electronics manufacturing industry.

In the competitive electronics manufacturing industry, the twin pillars of precision and accuracy are non-negotiable. The industry’s drive towards increasingly miniaturised yet powerful devices demands manufacturing processes of unparalleled precision. This precision directly influences a product’s reliability, functionality, and, ultimately, customer satisfaction. Herein lies the undeniable value of precision measuring instruments, tools that stand at the heart of quality assurance processes, ensuring every component meets the exacting standards demanded by the industry and consumers alike.

The Importance of Quality Control in Electronics Manufacturing
Quality control in electronics manufacturing is not just about adherence to standards; it's about setting the benchmark for product excellence. Across the globe, leading electronics manufacturing services showcase a profound commitment to quality, positioning themselves as leaders in precision manufacturing. This unwavering dedication is mirrored in the rigorous quality assurance measures adopted industry-wide, underscoring the indispensable role of precision measuring instruments. These tools are essential in ensuring product reliability and enhancing customer satisfaction, reflecting a universal ethos where excellence in quality is not just pursued but achieved.
Key Precision Measuring Instruments Used in Electronics Manufacturing
The electronics manufacturing industry relies heavily on precision and accuracy, not just as a benchmark for quality but as a necessity for functionality and reliability. In this context, certain precision measuring instruments have become indispensable tools, each serving a unique purpose in the manufacturing process, from design and development to testing and quality control. Here's a look at some of the essential instruments and their applications:
Callipers: These versatile instruments are essential for accurately measuring the dimensions of components and PCBs (Printed Circuit Boards). Callipers allow manufacturers to ensure that parts fit precisely as designed, a critical factor in the assembly of electronic devices.
Multimeters: Multimeters serve a critical function in assessing the electrical properties of components, including voltage, current, and resistance. Their versatility makes them a staple on the manufacturing floor, enabling technicians to diagnose problems, verify product performance, and ensure electrical specifications are met. Choosing the best multimeter, tailored to the specific needs of your projects, is essential for accurate measurements and reliable quality assurance.
Oscilloscopes: Oscilloscopes play a pivotal role in visualising electronic signals. They provide a dynamic view of signal voltage over time, allowing engineers to observe the behaviour of electrical signals within the device.
Micrometers: Micrometers are employed for their ability to measure small objects with exceptional precision, typically to the micron level. In electronics manufacturing services, they are used to ensure the precise fit of components, which is vital for the seamless assembly of intricate devices.
Data Loggers: Monitoring environmental conditions is crucial in electronics manufacturing, as variations in temperature, humidity, and other factors can significantly affect the manufacturing process. Data loggers are used extensively to record these environmental conditions, providing a continuous data stream that can be analysed to ensure the manufacturing environment remains within optimal parameters.
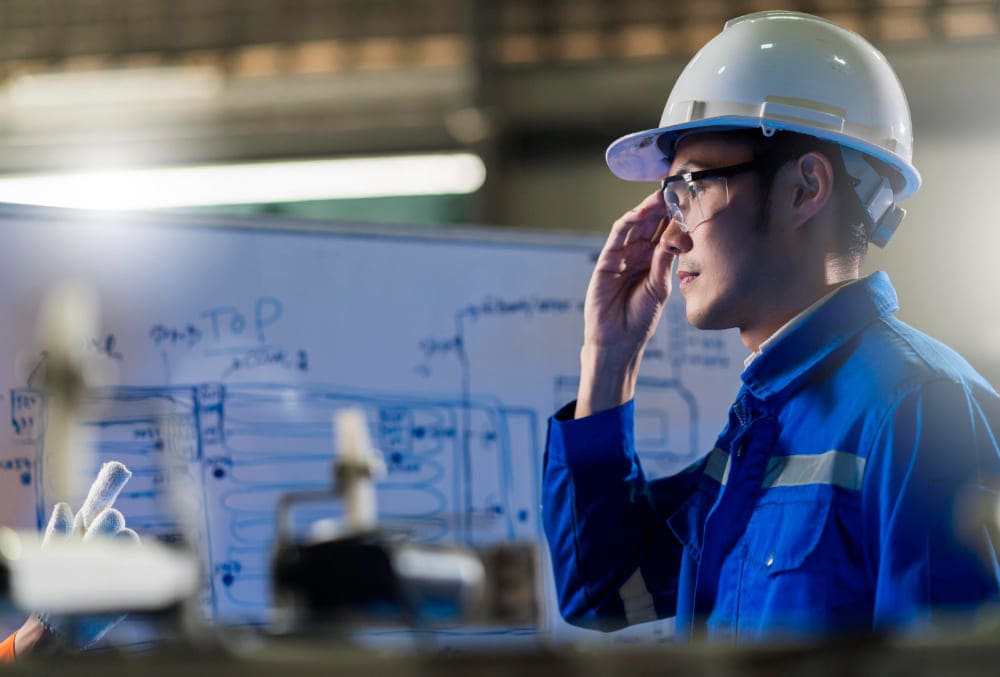
Adhering to Singapore's Electronics Manufacturing Standards and Regulations
Singapore's position as a hub for high-tech electronics manufacturing is not just a testament to its technological prowess but also to its stringent adherence to industrial standards and regulations that ensure quality and reliability. The foundation of this regulatory framework is the Singapore Standard for Quality Management (SS ISO 9001), which outlines the criteria for a quality management system. This standard is instrumental for electronics manufacturers, guiding the development of processes that consistently align with customer expectations and regulatory mandates, thereby ensuring product quality and reliability.
The Singapore Standards Council, alongside SPRING Singapore—now part of Enterprise Singapore—lays down comprehensive guidelines that span the entirety of the electronics manufacturing process, from design conceptualisation to the final delivery. These guidelines underscore the importance of rigorous quality management practices and detail the requirements for maintaining high production standards, emphasising the crucial role of industrial electrical safety in the process.
The application of precision measuring instruments is critical in adhering to these guidelines, offering the requisite accuracy and consistency for regulatory compliance. For example, oscilloscopes are indispensable in certifying electronic components against electromagnetic compatibility standards, while micrometers and callipers ensure component dimensions precisely match specified tolerances.
Implementing Precision Measuring Instruments in Quality Control Processes
Integrating precision measuring instruments into the quality control workflows of electronics manufacturing is a nuanced process that demands a strategic approach. These instruments are the linchpins of ensuring the production of high-quality electronic components, necessitating their seamless incorporation into daily manufacturing routines.
Best practices for this integration include the calibration, maintenance, and proper training of personnel in the use of these instruments, as these are foundational to guaranteeing accurate measurements. Calibration is a critical step that aligns the instruments with established standards, ensuring that their readings are precise and reliable. Regular maintenance schedules are equally important, as they prevent the potential drift in instrument accuracy over time, a common issue that can lead to significant discrepancies in measurement and, consequently, product quality.
Securing Excellence in Electronics Manufacturing with Precision Instruments
Investing in high-quality measuring instruments is not merely a matter of regulatory compliance; it is a strategic decision that directly impacts a manufacturer's reputation, customer satisfaction, and ultimately, its competitive edge in the global electronics market. Precision in manufacturing equates to excellence in product performance, which in turn fosters consumer trust and loyalty. In an industry characterised by rapid technological advancements and intense competition, the ability to consistently produce reliable, high-quality electronics is invaluable.
Keysight Technologies
Keysight Technologies is at the forefront of electronics manufacturing innovation, providing oscilloscopes that enable advanced circuit design and analysis.
Related links
- Fibre Optic Solutions for High-Speed Data Transmission in Data Centres
- Industrial PCs: Key Features, Uses and Computing Essentials
- WIKA Calibration Multimeter Software for Use with Pressure...
- Hanna Instruments Glass Measuring Cuvet
- How Electrical Insulation Adhesive Tapes Support Our Electrical Industries
- Norgren Sevice Kit
- RS PRO Adhesive Pre-Printed Adhesive Label-QA Seal-. Quantity: 200
- RS PRO Adhesive Pre-Printed Adhesive Label-QA Rejected-. Quantity: 140