- Published 8 May 2024
- Last Modified 7 Jun 2024
- 12 min
Everything You Need to Know About DIN Rails

What are DIN rails?
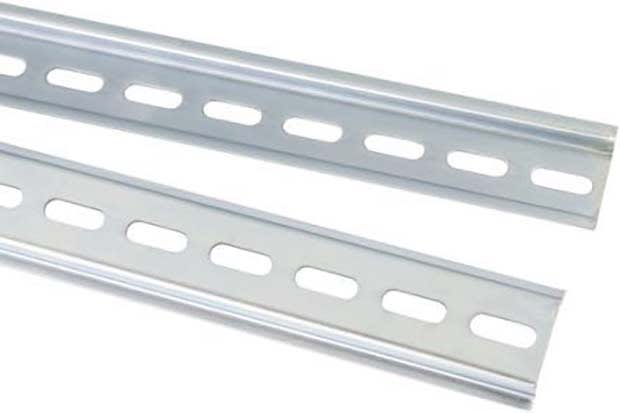
DIN rails are the long metal strips that form the core part of a global industry standard component rail-mounting system in equipment cabinet racks. DIN rails are designed for securely attaching electrical and industrial control products - such as circuit breakers, terminal blocks, power supplies, actuators, solenoids and so on - inside a typical equipment rack housing cabinet or frame.
In this context, ‘DIN’ is an acronym that stands for Deutsche Institut für Normung, which translates into English as ‘German Institute of Standards’. The now-familiar rack-mounting system we see supporting components of all kinds in many industrial settings was first devised by the Germans in the late 1920s. It was more widely adopted and developed into its current form during the 1950s, initially by neighbouring European countries and then quite quickly taken up worldwide.
DIN rails exist purely for the purpose of physical (mechanical) component support, rather than as any sort of connective or conductive element within a wider electrical system. In other words, they are not busbars, although they can perform a grounding busbar role in certain scenarios.
The advantages of a DIN rail system for mounting hardware components are numerous:
- They save time and work - components simply snap or slide into place on the rail, rather than having to panel mount each individual component separately.
- They save space - DIN rails allow for tight configurations of components and provide a convenient site for bringing internal and external wiring circuits together, ideal in limited space applications
- They’re cost-effective, both in terms of DIN rail pricing itself and the potential it offers for high-density adjacent mounting - this can significantly reduce the overall amount of wiring and cabinet space needed
- They promote neat and well-organised component layout, which is better for all-round safety and maintenance access
- They adhere to universal sizing and mounting protocols - see below
The real beauty of the DIN rail system is that it was designed (and has continually evolved) to work with to a series of universal standard widths and shapes of mounting hardware. The fact that DIN rail systems are today recognised as a range of fixed and consistent standards means that installers can be guaranteed dimensional uniformity across a whole suite of relevant products, regardless of whichever company is handling manufacture or supply of various individual parts.
This level of cross-brand compatibility gives users of DIN rail systems the flexibility to mix and match components, without having to stick to a single proprietary model range to get the job done. Proprietary systems do exist, but they’re less widely used for precisely this reason.
It’s worth noting that the naming conventions for DIN rail types and sizes might differ slightly from country to country. In the US, for example, you might be less likely to see the common UK name ‘top hat section’ used for standard 35mm DIN rails, and more likely to hear the same products referred to as TS35 rails.
However, these naming conventions are reasonably interchangeable and understood by most installers, and the mounting rail shapes and sizes they refer to will still be fully compatible. We’ll say a bit more sizing and compatibility in subsequent sections.
In the table below, we’ll look more closely at the main types of DIN rails you’ll find on sale for fitting components to a variety of PLC racks and enclosures, and find out more about exactly how these different grades and shapes of DIN rails are selected, mounted and used in a wide range of everyday workplace applications.
Types of DIN rails
The vast bulk of widely available DIN rail types fall into three or four key categories, largely defined by the physical footprint of the rail when viewed in cross-section.
Below is an example of a dimensional drawing for a 35mm Top Hat Slotted DIN Rail.
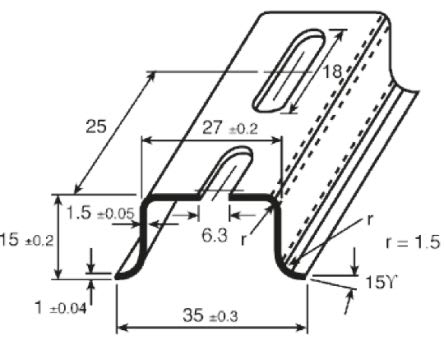
As such, one of the key things to bear in mind when looking to assemble or buy DIN rail systems is to make sure that you purchase rail sizes and types that will be compatible with the components you’re mounting. There is also a wide selection of DIN rail terminal accessories available to fit many systems for enhanced compatibility and functionality.
Numerous types of DIN Rail are available, many of which conform to European (EN) and international (IEC) standards. The main types and sizes include:
TS35 or ‘top hat’ sections (EN 50022)
Top hat sections are broadly considered the industry standard in DIN rail terms, and are the type you’ll likely find most readily available. TS35 DIN rail is very commonly used for mounting a wide range of of electrical industrial control products and components, from circuit breakers and motor controllers to remote I/O, transformers, drives and much more.
The ‘top hat’ naming convention refers to the fact that the cross-section of a TS35 DIN rail resembles the cross section of a deep hat (essentially a rectangular bowl shape), and they’re 35mm wide from edge to edge
Top hat din rails are available in the TS35 standard at channel depths of both 7.5mm (standard) and 15mm (‘deep hat’, or sometimes ‘high hat’). For a significant majority of everyday component-mounting needs, including many popular power supplies and circuit breakers, the 7.5mm versions of top hat or 35mm DIN rail will be broadly suitable.
TS15 or ‘miniature top hat’ sections (EN 50045)
As you might expect, the miniature top hat or TS15 DIN rails are the same shape as the above type, only smaller. The two standards differ predominantly in terms of their edge-to-edge width, with TS15 rails measuring just 15mm wide.
Their respective channel depths are often different too, with mini top hat varieties tending to be shallower than TS35 rails (around 5.5mm deep is a fairly common format). 15mm DIN rail is generally used wherever space is at a premium, or to mount smaller components such as compact junction boxes and relays.
TS32 or ‘C’ sections
Also following the above naming patterns, TS32 DIN rails are 32mm wide from edge to edge, and have a C-shaped cross-section with a symmetrical curve to their outer edges. This is generally seen today as an older standard of DIN rail mounting system, which was more common during the earlier years of universal adoption but has now been surpassed by the TS35 variant.
Where it is still used, it’s generally reserved for larger or heavier items such as power supplies and transformers, due to the excellent wall support it offers. For many modern components, however, an adapter will be needed to allow for properly secure mounting to a TS32 DIN system.
C-section DIN rails are usually categorised by the vertical height of the rail once mounted to a panel (C20, C30, C40 and C50 are the more common variants).
TS ‘G-type’ sections (EN 50035)
Again, G-type DIN rails (sometimes also known as J-type, depending on the precise configuration) are named for the shape of their cross-section, and feature a deeper recess at one side than the other.
The deeper of the two outer channels on a G-section DIN rail is usually positioned at the lower edge when the rail is panel mounted, offering additional support for any heavier or higher-powered components you may wish to attach.
Slotted or non-slotted DIN rail sections
Among most of the above rail size and shape types, another common variant to consider is whether you want your DIN rail slotted with pre-cut mounting holes or not. Most types of DIN rail will be available in both slotted and unslotted variants, potentially offering better system organisation, component support or overall flexibility depending on which you opt for.
DIN Rail Connectors
When it comes to connecting together the components arranged around your chosen DIN rail mounting system, there are various connector options available depending on the exact type of configuration and application you’re working with.
In this section, we’ll take a brief look at some of the more common DIN rail connector blocks and what they’re generally used for.
Din rail solenoid valves
Din connectors for hydraulic valves and solenoids are an important part of any system that incorporates valves of either type.
Similar to but distinct from hydraulic valves, solenoid valves are an electromechanical component acting as a functional interface between electrical or electronic control systems and pneumatic drives, using an electric current to generate a magnetic field and thus operate a mechanism. This allows for the automatic operation of the valve, without requiring an engineer to physically manipulate it themselves.
Solenoid valves are widely used in systems where the flow of very clean liquids, gases or light oils needs to be controlled and moderated. Today, many such products are configured for easy and convenient mounting to DIN rail systems, and these systems will require DIN connectors for solenoid valves to ensure reliable flow between the various components mounted along the system.
DIN rail solenoid valve connectors and hydraulic valve connectors are widely available in a number of configurations, most often fitted with either cable connection points or internal circuits. They tend to come in a variety of different thread styles, circuitry options and gasket types and very often include additional features such as certified IP ratings against dust and moisture ingress.
DIN rail terminal blocks
Perhaps the most common DIN rail connector type is the extremely widely used terminal block. As with the other connectors mentioned above, a DIN rail terminal block functions primarily as a linking and management/safety interface between different components and DIN sections arranged adjacently (or indeed spaced out) along any suitable DIN rail system.
DIN rail terminals are used to maintain complex control circuits in applications such as:
- Energy management
- Power supplies
- Lighting controllers
- Telecommunications
- Building management systems
- Industrial and civil electrical installations
- Heating and air conditioning controls
Terminal blocks for DIN rails are available across a very broad catalogue of types, configurations, functions and features. The range of configuration options usually includes screw, clamp and push-in terminals, with leading brands in the market including the likes of Weidmüller, ABB, Phoenix Contact and Wago.
In addition to the base units themselves, DIN terminals are often sold alongside an even broader array of DIN rail terminal accessories, offering many additional options for modularity and advanced functionality. This might include such products as:
- End and intermediate plates
- Fixed bridges
- Marker strips
- Partition plates
- Shield connectors
- Test adapters
- Jumper bars
- Support plates
- End sections
For any further advice on terminal blocks, how they work or what sorts of accessories might be most useful in your intended application, please feel free to contact a member of our expert technical support team any time.
DIN rail mounting
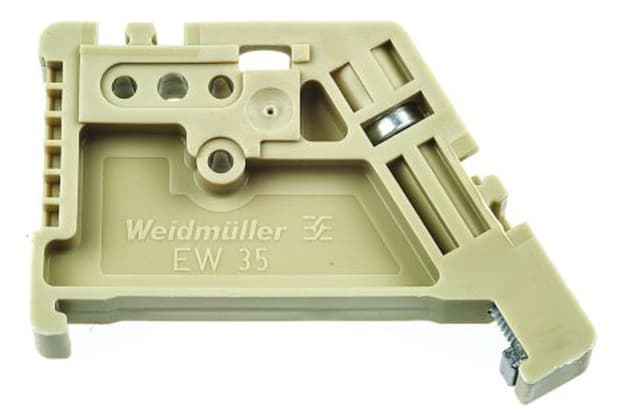
There are some key factors to bear in mind when planning and shopping for your DIN mounting rail setup - these are mainly based on:
- The precise application you have in mind, including the layout and combined weight of components along various stretches of the rail system
- The environment in which the system will be mounted and run
Much like the various options for DIN rail configurations and types, the physical mounting options for DIN rail systems themselves are fairly diverse, incorporating a range of common materials and bracketing types. Most suppliers selling DIN rail systems will also offer a variety of DIN rail mounting kits and accessories, which may include various sorts of mounting clips, brackets and end caps to help support the rail system holding your components within a rack cabinet or similar.
Environmental factors are especially important in selecting which type of DIN rail and mounts you’re going to install. Among other things, you’ll want to consider variables such as:
- Potential exposure to suboptimal ambient conditions
- Enclosure materials and panel construction
- Cooling availability and working temperature range of components
- Protection requirements
- Connections and wiring setups
- Additional functionality requirements
Broadly speaking, stainless steel DIN rails and mounting brackets are often considered among the most robust and reliable types in most applications, although they’re seldom the most cost-effective options. Zinc-plated steel variants are a very common all-rounder option that offer impressive stability combined with fairly cheap prices for basic setups.
However, more economical alternatives such as zinc-plated steel may not fare as well in humid environments where there’s a greater risk of corrosion - in that sort of scenario, anodized aluminium is a popular alternative. If a DIN rail system is also intended to function as a grounding busbar, then copper may be the best option, although this can come with some potential caveats regarding long-term rigidity and support strength under certain challenging conditions.
Summary
DIN rails and mounting systems provide the literal scaffolding that supports organised, clean, safe, efficient and - most importantly - universally interchangeable rack-mounting systems across a huge diversity of industries and workplace environments the world over. They’re very simple and user-friendly to install, and can enable installers to create an extremely cost-effective and space-saving solution for all manner of electrical and electromechanical systems that are reliable and easy to maintain over years of dedicated service.
As with all products designed around extensive modularity and infinitely swappable interfaces, though, it certainly pays to know a few key details beforehand - most importantly, a good understanding for the exact types of systems and components you’re looking to install via DIN rail mounts - before you take the plunge with a specific configuration of rails, terminals or accessories.
Related links
- DIN Rails
- Everything You Need To Know About O-Rings And Seals
- Electrical Tape Types & Alternatives Guide
- A Complete Guide to Socket Sets
- XP Power DIN Rail Mounting Kit, for use with ECE60 DIN Rails
- RS PRO Steel Slotted DIN Rail 2m x 35mm x 7.5mm
- A Buyer’s Guide to LED Tube Lights
- Rittal Sheet Steel DIN Rail, 2m