
Prevent & Predict Next Steps
Some great advice to help you minimise downtime.
Choosing the best preventative and predictive maintenance methods for the application is key to an effective maintenance strategy.
In today’s climate there are increased output pressures on manufacturing to keep up with modern demand - exacerbated in the post-pandemic world. Therefore, creating efficiencies is the Holy Grail, while unplanned downtime is the arch enemy. Those maintenance teams still operating on a reactive basis will undoubtedly fall victim to unplanned downtime – and the varied frequency and unpredictability of this will cause hindrance and detriment to any manufacturing operation.
With preventative and predictive maintenance methods and equipment, and advanced technology in the Industrial Internet of Things (IIoT) sphere now widely available, it’s difficult to know where to start or how to implement this in an effective maintenance strategy. So whether you’re at the beginning of your proactive maintenance strategy journey, or have made the leap and want to understand more about how to make use of the many aids available, we’ve highlighted some of the key considerations.
Monitoring is key to effective maintenance
Preventative maintenance methods such as calendar or usage-based planned interventions are effective in helping to prolong the life of equipment and minimise risk of unplanned downtime. This can include activities such as applying lubrication at the right intervals, and replacing parts prone to failure. Additionally, upgrading components to more durable solutions can help avoid interventions. For example, replacing electromechanical relays with solid state versions, fitting anti-vibration mounts to reduce wear damage and fitting air pressure regulators to save energy and extend component life are all effective, relatively low cost and sensible measures to take.
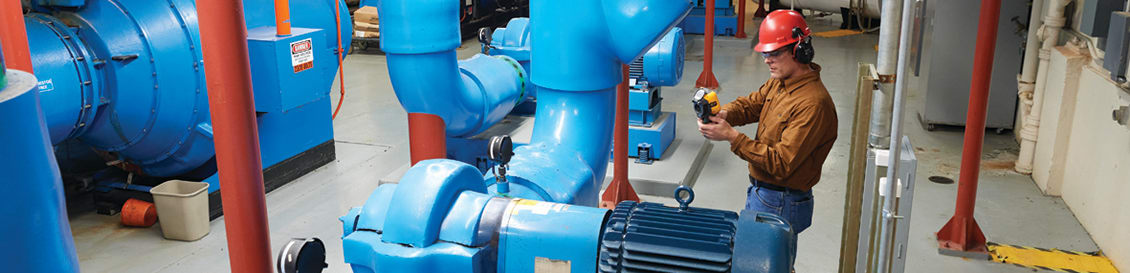
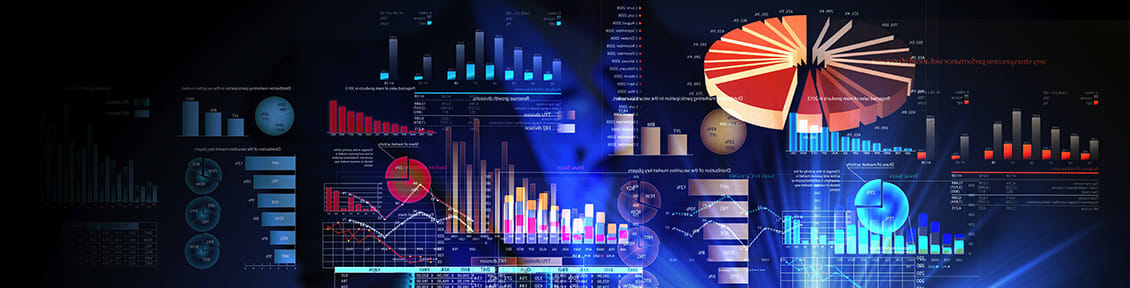