- Published 30 Jul 2024
- Last Modified 8 Aug 2024
- 9 min
Sprocket Essentials: From Basics to Advanced Tips
This guide covers what sprockets are, their various types, how they function, and tips for selecting the perfect sprocket for your chain.

Overview of Sprockets and Their Uses
A sprocket is a mechanical wheel with teeth designed to engage with the links of a chain or belt, facilitating the transfer of rotational motion. Unlike gears, which mesh directly with one another, sprockets work exclusively with chains or belts, requiring both components to have matching pitch and thickness for optimal performance. This unique design allows sprockets to be used in various applications, including bicycles, motorcycles, and industrial machinery.
Sprockets are typically made from durable materials like steel, which enhances longevity and wear resistance, making them suitable for heavy-duty applications. In contrast, aluminum sprockets are lighter and often used in high-performance vehicles like motorcycles and bicycles, although they may wear out more quickly than steel. The choice of material depends on the specific needs of the application, balancing weight and durability.
Modern sprockets incorporate advanced features such as hardened teeth for increased wear resistance and special coatings to reduce friction. These innovations help improve efficiency and extend the service life of sprocket-driven systems. Understanding sprockets is essential for those involved in mechanical engineering and vehicle maintenance, as these components play a crucial role in the functionality of many machines in our daily lives.
Key Components of a Sprocket
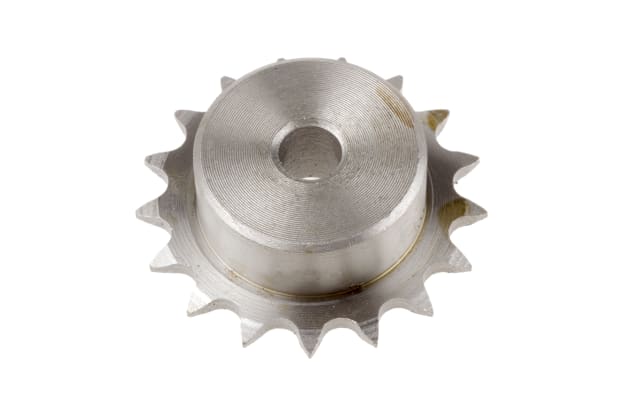
Each sprocket has several important characteristics that determine its functionality and compatibility with chains or belts:
Number of Teeth: This refers to the total count of teeth on the sprocket, with each individual tooth engaging with the links of a chain or belt. The number of teeth affects the sprocket's rotational speed and the torque it can transmit.
Pitch Diameter: This is the diameter of the sprocket measured at the point where the chain or belt engages with the teeth. It is crucial for ensuring that the sprocket and chain or belt work together smoothly. The pitch diameter influences the overall size and fit of the sprocket within a mechanical system.
Outside Diameter: This measures the diameter at the tips of the sprocket's teeth. It is essential for determining the sprocket's clearance and ensuring it fits within the designated space in a machine or vehicle.
Pitch: The pitch is the distance between corresponding points on adjacent teeth, usually measured in inches. It must match the pitch of the chain or belt to ensure proper engagement and efficient power transmission.
Sprockets are often made from durable materials like steel for longevity, though aluminum is sometimes used for applications where weight reduction is important, such as in bicycles and motorcycles.
Common Sprocket Types and Their Applications
Sprockets are essential components in various mechanical systems, available in diverse shapes, sizes, and tooth configurations. Each type is designed to meet specific operational requirements and enhance system performance. Here's an overview of common sprocket types and their applications:
- Double Duty Sprockets: These feature two sets of teeth per pitch, allowing for extended use. When one set wears down, the chain can be advanced to engage the fresh set, effectively doubling the sprocket's lifespan. This design is particularly useful in high-wear environments or where frequent maintenance is challenging.
- Hunting Tooth Sprockets: Characterised by an odd number of teeth, these sprockets distribute wear more evenly. Each revolution engages a different set of teeth with the chain links, reducing the frequency of contact for each tooth. This design significantly extends the sprocket's service life, making it ideal for continuous operation systems.
- Segmental Rim Sprockets: These sprockets feature replaceable rim segments, typically in three, four, or more pieces. This design allows for rim replacement without removing the chain or dismounting the entire sprocket, significantly reducing downtime during maintenance. They are particularly valuable in industrial settings like elevators or conveyor systems where minimising operational interruptions is crucial.
- Multiple Strand Sprockets: Designed for applications requiring higher torque and power transmission, these sprockets can accommodate two or more chains simultaneously. They're commonly used in heavy-duty industrial machinery or where multiple components need to be powered by a single drive shaft, ensuring synchronised operation.
- Quick Disconnect (QD) Sprockets: These sprockets are engineered for easy installation and removal, making them suitable for applications with higher working loads. Some models offer reverse mounting capabilities, providing flexibility in system design and maintenance. QD sprockets are particularly useful in environments where frequent adjustments or rapid equipment changes are necessary.
- Idler Sprockets: Used primarily to manage chain slack in long chain runs, idler sprockets help prevent chain whipping and ensure even load distribution. They're also employed to guide chains around obstructions, maintaining proper tension and alignment throughout the system. Idler sprockets play a crucial role in optimising chain performance and reducing wear in complex mechanical setups.
- Split Sprockets: Designed for easy installation in tight spaces or where shaft disassembly is impractical, split sprockets come in two halves that can be bolted together around the shaft. This design significantly simplifies maintenance and replacement procedures in complex machinery.
Pilot Bore Sprockets
Common in industrial machinery, bicycles, and motorcycles, these sprockets feature a cylindrical projection that can be drilled to the required bore size. This design allows for precise fitting to shafts and can be secured using various methods such as grub screws or locking bushes.
Taper Bush Sprockets
These sprockets have a split design through the taper and flange, creating a clamping effect on the shaft. They utilise standardised taper bushes, making them versatile for fitting various shaft sizes.
How Do Sprockets Work?
A typical sprocket system consists of two sprockets connected by a chain or belt, with one acting as the driver and the other as the driven component. As the driving sprocket rotates, it engages the chain or belt, transferring power or altering the torque and speed of the mechanical system. Larger sprockets with more teeth can handle heavier loads but generate more friction, potentially reducing operational speed. Regular maintenance is crucial, as worn sprockets with sharpened or hooked teeth need replacement to ensure optimal performance.
Sprockets find widespread use across various industries and applications:
- Bicycles: They convert the rider's pedaling motion into wheel rotation.
- Tracked vehicles: In tanks and agricultural machinery, sprockets engage with track links to facilitate movement across uneven terrain.
- Film equipment: Both cameras and projectors use sprockets to precisely control film movement.
- Industrial machinery: Conveyor systems and other manufacturing equipment often rely on sprocket-driven mechanisms.
Choosing the Right Sprocket for Your Chain
Sprockets come in various configurations to match the specific requirements of the chains they work with. They are available with one, two, or three rows of teeth, corresponding to simplex, duplex, or triplex chains. Simplex sprockets are the most common, accounting for about 70% of market applications, while duplex and triplex sprockets cover approximately 25% and 5%, respectively.
Standards and Chain Sizes
The two primary chain standards in the market are the British Standard (BS), also known as the European Standard, and the American Standard (ANSI). Each standard has a range of chain sizes, typically denoted with a number followed by a hyphen and another number indicating the number of strands. For example, a '12B-2' chain requires a duplex sprocket. These standards ensure compatibility and performance across different applications.

It's important to note that although these products are often measured in inches, they are sometimes converted to metric dimensions to suit European markets. This conversion is also true for chains and hydraulics. When selecting a sprocket, you need to determine the size, outside diameter (OD), and the number of teeth to establish the force ratio and ensure proper fit and function.
Calculating the Sprocket Ratio
The sprocket ratio is a critical factor in determining the performance of your mechanical system. It is calculated by dividing the number of teeth on the driving sprocket by the number of teeth on the driven sprocket. For instance, if the driving sprocket has 20 teeth and the driven sprocket has 60 teeth, the sprocket ratio is 20/60, which simplifies to 1:3. This ratio indicates that the driven sprocket will rotate once for every three rotations of the driving sprocket, affecting the speed and torque of the system.
Gears vs. Sprockets: Key Differences and Applications
Gears and sprockets are both essential components used to transmit power in mechanical systems, but they operate in fundamentally different ways. While they may appear similar, their design, function, and applications distinguish them from each other.
Feature | Gears | Sprockets |
---|---|---|
Function | Transmit power by meshing directly with other gears | Transmit power through a chain or belt |
Design | Teeth can be on the outer and inner circumferences | Teeth designed to fit precisely into chain links |
Operation | Work together to create a network of movement | Operate more independently to move chains or belts |
Torque Handling | Can handle higher torque due to direct meshing | Suitable for lower torque applications but effective for longer distances |
Applications | Used in automotive transmissions, industrial machinery, and precision devices | Commonly found in bicycles, motorcycles, and conveyor systems |
Wear Patterns | Higher wear due to direct contact; may require more maintenance | Subject to wear from chain engagement; easier to replace |
Maintenance | Requires careful inspection and alignment | Regular inspection needed to check for chain slippage and tooth wear |
Sprockets
Often referred to as a chain wheel, is a mechanical component designed to transmit rotational motion through a chain or belt. Unlike gears, sprockets do not interlock with each other; instead, their teeth fit into the links of a chain, allowing for efficient power transfer. Sprockets are commonly used in bicycles, motorcycles, and various industrial applications, where they help drive machinery and convey materials. They come in different types, such as simplex, duplex, and triplex, to accommodate various chain configurations.
Gears
A wheel with interlocking teeth that mesh with other gears to transmit power and motion. Gears are designed to work together in a system, allowing for the transfer of rotational movement, speed, and torque. They are essential in various mechanical applications, including automotive transmissions, machinery, and robotics. Gears can change the direction of movement and are available in different sizes and tooth configurations to achieve specific mechanical advantages. Their precise alignment and meshing capabilities enable efficient power transmission in complex systems.